
The Factory trip for Wooting one
May 9, 2016
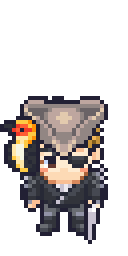
Calder
I remember when I started working for a Taiwanese manufacturer and visited all different types of factories and was awe-shocked/fascinated at how things were really made.
It's like you’ve always believed everything magically appeared or was made in these fancy, clean and high-end factories you see on TV but then realize that it was all propaganda by your parents or evil marketing people.
We feel it's good for you to also understand and see more about what happens behind the scenes and how the Wooting one is made. The real deal.
I just came back from my factory trip in preparation for mass-production. This will give you a preview of the production process. I hope to show you more when the actual Wooting one is made for you.
The Flaretech Switch Factory
The Flaretech switch is an essential part of the Wooting one, it is a bit different from your regular switch, being optical and all, but other than that it’s assembled like a regular switch.
The smaller components are produced and then assembled in an automated machine. It's literally hypnotizing to see the machine at work.
Tooling & Injection Factory
To make the bottom case and keycaps in mass production, it needs specific tooling (molds). The bottom case particularly will be plastic injected into a big mold in the shape of the case.
After the main body is CNC machined (a big cutting machine that can sculpture things out of metals) it goes in, what they call, the spark machine. It makes the finer/minor adjustments in the mold.
Keycaps-wise (for backlit keyboards) you’ll often find a single ABS injected blank version that is first coated black, then lasered for the legends, and UV coated. This makes it easy and affordable to make customized legends on backlit keycaps.
Extra info:
If you ever wondered why double injection ABS or PBT keycaps are so expensive, it’s because a double injection means you’ll need to make two molds for every single keycap (twice the cost) and the legends are permanent for the molds.
Then for PBT, this plastic material is very tedious because it tends to shrink a lot in different variables after injection. It means the environment needs to be extremely well controlled.
Assemble, QA and main factory
Everything comes together in the main factory for assembly and quality control. So here the Wooting one will be assembled, tested, packaged and boxed for shipment.
This factory strictly follows a Japanese methodology from cleanliness to extremely organized and separated processes.

I wasn’t allowed to record anything inside, where all the magic happens, but it was literally mind-blowing impressive how professional they go to work. I say this with quite some experience with different factories over Asia.
Non-surprising they are pending the 7th year of role model factory for Panasonic car accessories (i.e., a major feat in manufacturing terminology).
All the quality testing also happens in this factory for keyboards and mice. On its way to 100 million clicks for on the Flaretech switch.
Preparations for Kickstarter
Along the way, I was also able to collect different missing parts of the final Prototype. We’re doing our best to give the most accurate representation of the Wooting one at the Kickstarter launch but we don’t want it to delay everything anymore.
It's more important that you get the Wooting one in your hands as soon as possible at a non-compromising matter.
Join the conversation
Hopefully, this gave you a better picture of how things work and I can’t wait to share about the actual production. If you have questions or would also like to share your experience, you're welcome to:
- In the comments below
- On Facebook /wootingkb
- On twitter @wootingkb (can also dm)
- By email social@wooting.io
© 2025 Wooting technologies版权所有。