
No more vaporware | Lekker update #7
October 5, 2020
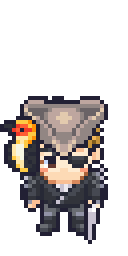
Calder
Hello world…. This is Calder writing an overdue Lekker update using my Wooting two Lekker Edition and it’s working like a charm. In this update:
- The EVT sample
- The Schedule
- Bottom-case status
- PCBA status
- Software development
Let’s first appreciate and enjoy the typing sound on the Wooting two Lekker Edition:
Typing on the Wooting two LE is an absolute pleasure. The sound is very suppressed, it feels extremely smooth, and there is absolutely no ping present. Deciding to work with Gateron, best decision ever. The stabilizers and switches both come pre-lubed. I can also confirm now that it has a foam pad underneath the PCBA to further suppress noises.


Simon rounded up the Wootility connectivity with the Wooting two Lekker Edition, and I was able to get started playing around with RGB. Compared to the Flaretech keyboards, the RGB lighting is much more out there. It’s an inherent effect of the switch design. Love it or hate it, it’s really cool to see the entire switch light up.
We made custom software for production that flashes the firmware, tests the LED, and allows you to inspect the analog input values. These values at the moment aren’t tuned yet but can give insight on the raw analog input curve. In the video, you can see as I press the different buttons, the values change based on press depth. Except for numpad *, that one is going through a small test I haven't finished yet.
If you dial up the brightness to the max, it can even shine through the white PBT keycaps. However, if you’re smart, you can also tune the LED according to the keycap colors and it’ll blend away.
I had also taken apart the entire keyboard and inspected every part to see if there were any noticeable issues. Everything checked out, and Kevin’s endless work on the mold changes has panned out really well. I was worried that an SMD component or switch prong would collide with the bottom case. Now it’s all cushioned into a foam with enough clearance from the bottom case. It’s all A-OK.
I had also received the final braided cable. It’s thicker than our previous cables, it is rigid yet still flexible enough to manipulate without causing any kinks. The colors turned out great, it fits perfectly into the cable gutter. The quality is top-notch, sometimes I even forget the header is completely made of aluminum. Really glad about the result.
Jeroen also received a final EVT sample and we both noticed one issue that we’re still checking on. The switch plate, or top plate, is too dark. The navy blue is so deep, that it doesn’t really jump out anymore. When I compared it with my original prototype, you can see there’s a clear difference.
Note: the bottom case is not the final color, the black sample injections were used, as the EVT sample focuses on the function not appearance. Left is EVT sample - Right is old prototype.

It’s funny because we’ve gone through multiple samples and really tried our best to nail the color. We even paid for a separate color tank and only plan to produce this small quantity with it 🙃. Not sure if we slipped up somewhere or if the supplier did. Kevin has a signed plate that can confirm the color. If the signed plate matches, then there’s no more going back. It'll stay the same. If it's different, then we have a chance to address the issue. There's "we changed our mind", that'll set us back 2-3 weeks making samples, signing, and a supplier that'll go crazy.
The EVT sample even included the final packaging. This is usually not included during EVT, but we’re ahead of the formal development phases (more on this later).
I’m not allowed to show the packaging, it has to stay a surprise. However, the packaging is bad-ass and you'll probably keep it somewhere. There were two minor mistakes, such as a print on the inside and graphic on the inner box being rotated 180 degrees. Kevin will receive a final version, that should address these issues. However, if it's not the case, we'll just have to deal with 1000 head scratches, nothing worth changing if it causes any delay.
The manufacturer had also inspected the EVT sample and there’re a few minor changes required to ensure a smooth production:
- Minor change to the standoffs in the bottom case to better confirm the manufacturer’s standard screws.
- Minor change to the PCB holes to create a tighter assembly fit.
- Minor change to the PCBA routing around the screw areas just-in-case to ensure there’s no external noise that can impact the signal.
The first two require the Wooting two mold to move to our new manufacturer, and the last change is finished. More on this later.
What does this mean?
The engineering validation test (EVT) is a short phase to find any functional, electronic, or mechanical issues before going into Design Validation Testing (DVT).
DVT includes in-depth performance, mechanical, and conformance tests (humidity, temperature, water). The DVT phase also requires a lot more samples for testing and payments for 3rd party lab certification. And if the sample doesn’t pass the certification, they don’t refund the cost 😅. It's s more costly phase, and you’d want to remove the obvious beforehand.
After DVT, we’ll go into what’s called production validation testing (PVT). This is what we always refer to as the trial production. It’s when the manufacturer runs a production run for about ~5-10% of the order total for review. This is a moment they can further optimize and address any final issues that might occur. Then it goes over to the formal mass production and everybody starts crossing fingers.
Can you smell it yet? It's coming.
The Schedule
The new manufacturer working method is a degree more formal and bureaucratic than our previous manufacturer. This slows down the process, but at the same time makes sure we don’t screw up big time. It’s easy to miss something when there are so many moving parts. The last thing we want is to rush into production and find a critical issue. I have experience. Wooting one shivers 🥶. Due diligence by both parties is important.
The working method has also derailed my estimations a bit. I wasn't completely sure what their process would look like yet. This doesn’t mean that they’re causing a huge delay, not at all, but with all the formal processes it does mean that small mistakes, miscommunication, or changes result in longer lead times.
What has definitely caused a delay is the whole mold thing and the PCBA. More on this later.
We’re going to start DVT on the 26th of October. This will decide if we get the green-light for production. The manufacturer will plan a trial and mass production date (MP). Usually, this is also when they will start purchasing the parts for MP.
We had already started purchasing a lot of the essential parts in advance. Now with the EVT sample, we’re able to confirm the last parts and start purchasing more ahead of DVT.
The MP date will depend on when we receive all the required parts. The manufacturer confirmed that we should have all the electronic parts by the end of November. Electronic parts can be pesky, our quantity requirement and parts choices aren’t all available off-the-shelve. All the remaining (mechanical) parts, from my estimation, should arrive around the same time.
I was secretly hoping we’d go into mass production by November and still deliver in December. But if you’d ask me now, I can only say with confidence that mass production will happen in December. Then it goes onto a boat and we receive it in our warehouse somewhere mid to end of January.
Now that everything is getting more concrete, it’s easier to tell what the schedule will look like. Even though it still means that it’s going to take a little longer. The take away here is that it’s not baked air estimations anymore. A lot of the checkmarks on the list are checked off and this huge monster of a challenge has become smaller and smaller.
The Bottom case mold
Did you know we opened an entirely new mold part for the Wooting two> Just so we could fit in the Gateron x Lekker switches? I still can’t believe it.
When we started the project, the whole idea of using the Wooting two molds was to significantly reduce development time and reserve all margin for (unexpected) investments in the switch development. This has definitely flipped around.
In the previous update, the manufacturer accidentally damaged the new mold, causing a smudge on the injected part.

They were quick to repair it and continue with the first trial injections (T1). These T1 samples were sent to us for confirmation.
We were overall happy with the T1 samples, but we found a few small issues.
- The inside corners were not rounded.
- The USB-C port opening was a little jagged (damage or wear).
- The tolerance gap between the switch/top plate and case around the edges.
The first two issues were easy to change. The tolerance issue, however, was more tricky. The Wooting two has always had a small gap between the top plate and the bottom case. There’s a very small tolerance all around the edge, and it’s never 100% equal. This is extremely difficult to control and doesn’t only depend on the quality of the mold, but also the person operating the machine.
Kevin and I thought, you know, since we’re opening a new male-side mold, it’s an opportunity to make an improvement.
This kind of blew up in our faces and caused everything to delay by nearly a month. It’s a mix of things. They wanted several samples from the original mold to test the fit and compare it with the new mold. I had sent it over, to hear a week later that they needed all the components to install an entire keyboard. I had sent this over. 2 weeks later and a lot of asking, we received feedback. They weren’t able to improve it.
We quickly decided to let this go, and continue with fixing the other points. It took a long time for them to go through with the changes and make the second samples run (T2). In their defense, they are working with overcapacity and can’t dedicate a machine for a small sample run at all times.
We were quick to approve the T2 samples, it all worked out well. We immediately started with the formal process to move the mold. It took a little while to get an agreement on the conditions, but our new manufacturer will inspect the mold and complete the pickup on the 8th of October. Great news 👍. Tick this off.
No, untick it, please. As indicated in the introduction, the new manufacturer wants to make a few small changes to the mold before they bring it into production. It’s mostly for conformity with their standard parts and easier assembly. This will happen relatively fast and all within October before DVT. Semi-tick this?
The PCBA
Two updates back, I said the same thing, it always feels like the PCBA is almost done, but then it isn’t. The development before making the prototype PCBAs went on much longer than expected. A lot of the changes were related to preventing any kind of electromagnetic interference (EMI).
When it was finally over, we still had to wait a while for the prototype. To cut time, we also made the EVT samples at the same time.
When Jeroen received the prototype PCBA early September, he found three (minor) issues:
- The USB port was mirrored.
- An accidental routing line connected two keys.
- A capacitor value was too high causing higher input delay than we’d like to see.

These were all manually fixed for our EVT samples. The first two issues were obvious. The latter was a bit more tricky. Here’s an oversimplification.
Unlike the Flaretech optical switches, we need to deal with more signal noise coming from the sensors. The filter process is a balance between signal resolution and input speed. The more we filter, the more delay it introduces, the less we filter, the lower the signal resolution. The solution we had in place had great signal resolution and was far below the <1ms benchmark. However, it unexpectedly caused a signal delay differently.
Pressing a single key, everything works as expected. But if you’d press multiple keys at the same time it would introduce a small delay for each additional key pressed. To the point that pressing 5 keys at the same time, you’d surpass the 1ms input delay. If you’d theoretically press 100 keys at the same time, it would create an input slug. This behavior is not necessarily an issue, but the amount of delay each key added was not ideal. We could do better.
Jeroen spent some significant time researching the phenomena and came to the conclusion that by changing the capacitor we could significantly decrease the delay without sacrificing signal resolution.
Now you’re able to press 10 keys at the same time and it’ll still be within the 1ms benchmark. You know, the total amount of fingers on your hands 🖐 . It doesn’t matter how fast you can type, switch between keys, or if you're rank 1 OSU!, it has zero impact on delay. Only if you simultaneously press more than 10 keys and hold them all pressed, we can’t guarantee our <1ms input speed claim. It’s still NKRO.
To put things in perspective, there’s this huge green company with expensive optical switch keyboards that don't register more than 6 keys pressed at the same time. Coupled with the claim that the input runs at the speed of light, I'm not sure if we can beat that, or any other dissuasive marketing claim out there 😏.
Jeroen has a few ideas on how we can make improvements in the design to further bring it down, but it will require more time to research without any guarantee that it’ll work. This is honestly a never-ending story. At some point, we just have to call it and leave further improvements to the next version.
Software development
Software. Software. Software. Without good software, your hardware is pointless. It’s now extremely relevant for the development, from the manufacturing to the end-user experience. Jeroen and Simon are on it 👍 .
Simon, now officially part of the Wooting team and working full-time with us (yay!), is working with full-time dedication on the LE firmware. I don’t think we’d be in a good place without Simon. He’s a cool dude, knows his stuff, and is making heaps of progress.
Simon finished all the firmware fundamentals and now he’s working on making it all interactive and optimizing. There’s already one fundamental difference in the new firmware, how we deal with memory.
While Jeroen and Simon worked on adding the huge 16MB flash memory, they got a chance to revise how memory works on Wooting keyboards. The result is a more dynamic way to choose what functionalities you’d like to see on a per profile basis. It’s a bit too much and too early to share in this update alone, but it’ll give you a lot more control and makes it easier to deal with different memory sizes.
Another important milestone is the software used during production. It has multiple functions:
- Flash firmware on the keyboard.
- Flash keyboard serial number on the keyboard.
- Visual representation of analog signal per key to analyze issues.
- Quality control per key analog input signal.
We were not able to use the same software as the Flaretech keyboards anymore. Not that it was completely different, but Jeroen is much more experienced by now and he simply decided it was better to rewrite the whole thing. This is in my opinion a good sign of how we’ve built a wealth knowledge and specialty within Wooting. People are the assets.
Anyway, he finished the rewrite and it’s now used to analyze the keys. We’re still figuring out a good specification for the analog signal quality control. This also depends on how we deal with calibrating the keys.

So, let’s tick off programming the additional flash memory and production software from the to-do list. What remains:
- Analog signal calibration method for production and end-user
- Implementation of Rapid trigger in the Wootility.
- Implementation of a larger analog range in Wootility with additional tweaking options.
This is what we had set out as the minimal viable product (MVP) for the Wooting two Lekker Edition release. I’m very confident we'll deliver on software when you receive the keyboard. Whatever else we develop in addition to the MVP will probably end up in the (open) Wootility Beta or (closed) Wootility Alpha. No more fast public releases, stability comes first 😅.
Soon is becoming real
Okay, I hear you. We’re not completely on schedule. When I made that schedule, we were amid this huge leap from the completely unknown to the somewhat known. I was starting to get grip on the whole project again and our wild decision to go with Gateron was turning out well. The schedule estimation was still very early and aimed at delivering within this year.
Over the last few months, everything from the previous update started to materialize, a great morale boost for all of us. There was of course the usual “stuff” that just happens when there are so many moving parts causing mini delays. But it all added up to one thing: It’s becoming real.
You don’t want to know what a huge mental relief it was to receive that EVT sample and type on it. We’ve worked on this project for nearly 2 years, long before we released the pre-orders. It means everything to Wooting and brings us a step closer to our goal. I never expected it to take such a wild turn and take so long. A relief, I tell you, a relief.
The mass production is still going to be a challenge, now especially with COVID-19, we can’t visit the factory. We’ll rely on a third-party quality inspection company and remote problem-solving. Not ideal, but we didn’t start working with this new manufacturer if we didn’t believe they’d not be capable or reliable. In fact, they are a level up in quality and cost 😂.
Thanks a lot for your patience, hang in there a little longer, and remind yourself: Wooting always delivers.
<3 Calder
© 2015 - 2025 Wooting B.V. All rights reserved.