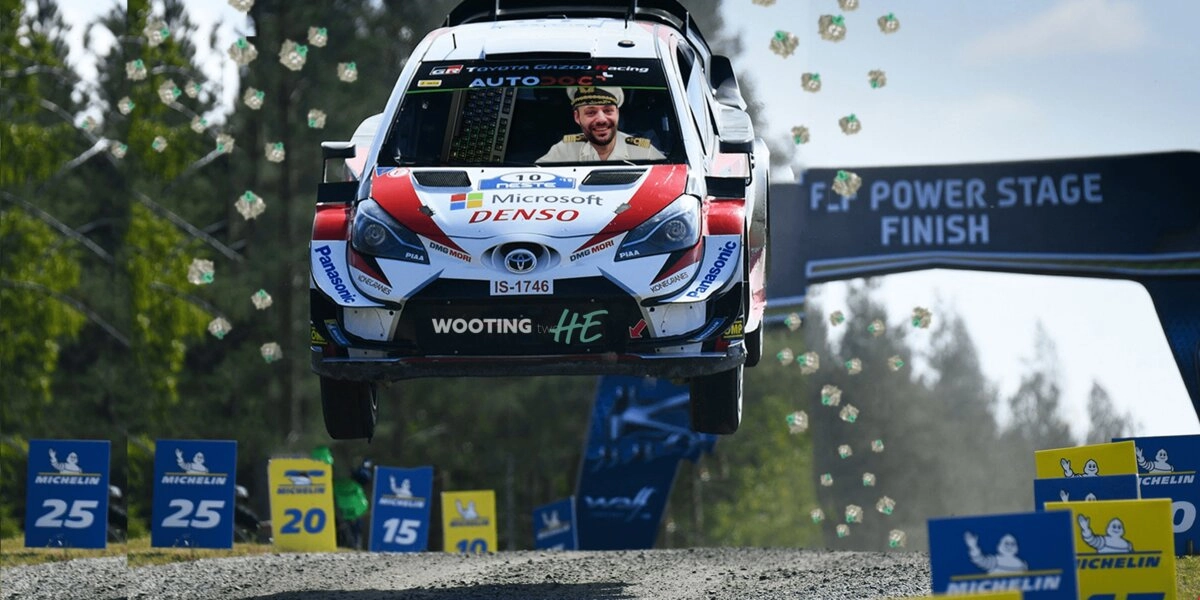
BUCKLE UP | WOOTING TWO HE | UPDATE #2
April 22, 2021
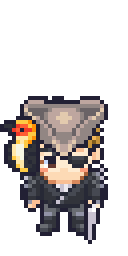
Calder
This is the first written update for the Wooting two HE, if you’re new to these updates, buckle up, you’re in for a ride.
When we were close to mass-producing the Wooting two LE (the limited edition predecessor, delivering soon) and launched the Wooting two HE, we had made all the proper preparations:
- Semi-finished the packaging design, just needed to sign off details.
- Started building a new PCBA prototype that would save a few components and lower cost.
- Placed purchase orders for the uncommon and most essential IC parts (hall effect sensors).
Since almost everything is the same for the Wooting two HE compared to the Wooting two LE – I thought this would be a straightforward and not too difficult process. Easy to predict a shipment date. But we have some type of omen that challenges us every step of the way. It’s incredible how complicated and challenging this whole business and process is.
How are we still around?
Plain and simple - You - believe in what we do and have the patience for us to figure it all out and deliver.
It started with the Wooting one, then two, and big-time with the Wooting two LE. The Wooting two LE status? Remember that Suez canal situation? That just delayed the boat shipment to the EU by about a month. This comes on top of all the other challenges these backers already had to endure during development. Really, a lot of love if you’re one of them reading this.
Yep, I’m warming you up. The Wooting two HE is going to be a little more bumpy than expected and I'll write a few more updates than expected. I’m going to cover the following:
- The top plate manufacturer challenge (solved?)
- The procuring IC parts challenge (pending)
- .Are you in Batch 1 or 2 and when you can expect delivery
- What we’re going to do to ensure faster delivery (Airfreight option)
Let’s get into this
A glossary
Before we get into the meat of the update, you need to educate yourself a little on the terminology and process of manufacturing a keyboard. If you know your stuff or read the previous Lekker updates, you can skip this.
You can break down the product development into 4 departments.
- Mechanical hardware
- Electronic hardware
- Software development
- Packaging & logistics
Not all companies deal with all these developments, for example you can purchase semi-finished products from an original design manufacturer (ODM). The manufacturer will have already covered the mechanical, electrical, packaging, and optionally software development. You'll only need to concern yourself with sticking on all the branding and dealing with the logistics. When you read people say it's an "OEM" product, they often mean this particular type product.
In our case, we work together with sub-contract manufacturers to develop a product from scratch and cover all 4 departments. When this is the case, you're exposed to much more elements of development and need to consider a ton more requirements. In the case of the Wooting two HE - we have already gone through all the major developments and most of it comes down to fine tuning parts for another mass productions.
Before we can go into mass production, we need to make 100% sure that the keyboard has no issues. Otherwise we'll end up with thousands of defect keyboards that we'd need to discard. This is why it goes through multiple rounds of scrutiny:
- Prototyping
- Engineering Validation Test (EVT)
- Design Validation Test (DVT)
- Production Validation Test (PVT)
Prototyping
This is usually focused on the electronic components and general functionality of the keyboard. The prototype phase allows us to skip a lot of formalities and quickly produce results before going to EVT.
Engineering Validation Test (EVT)
EVT is focused on the final electronic and functional design that are required of the keyboard. It'll also be the first soft-check for all the mechanical parts, but isn't a good representation, as the sample quantity often is too small for reliable results.
It's not safe yet to start purchasing all the required components for mass production.
Design Validation Test (DVT)
DVT has a larger quantity sample keyboards to test all the mechanical parts and it's soft-check if all the electronic and functional design is still working as expecting. These samples are also used for all the environment, drop, and operational tests. If there's also no issues detected in the electronic design, it's also sent for CE/FCC licensing.
At this point it should be safe to start purchasing all the required components for mass production.
Production Validation Test (PVT)
PVT is a pre-production run focused on the assembly process. This is when any remaining issues can be spotted that might hold up the production and the factory can optimize the assembly process.
Mass Production (MP)
The magic moment, all the quantities are manufactured. After this process is completed, you won't need to go through all the previous steps anymore to manufacture the keyboard. Unless you make significant changes to the design, packaging, or electronics.
Furthermore, there's a few more terminology used:
Lead times
The time between placing an order and delivery of the order.
PCB(A) - Printed Circuit Board (Assembly).
When it includes the A, it means the IC parts were also soldered to the circuit board.
Integrated Circuits (IC)
This is a miniature circuit board that’s compiled and packaged onto a small semiconductor to perform a specific task. When more complex, it’s often known as chips or microchips.
The top plate manufacturer challenge
When we went into the Wooting two LE production, we found that the top plate (the front-facing aluminum plate with the switches installed) wasn’t completely flush installed onto the bottom case. This was already the case with the Wooting one and two, part of the challenges with a floating design. However, since we made modifications to the Wooting two bottom case mold, it was a bit more noticeable.
We still continued with the Wooting two LE production since it had zero impact on performance and it’s easily dismissed while in use. This weighed in heavier than delaying it for another 2-3 months.
With the Wooting two HE, we had planned to have this issue resolved. We were already inspecting and discussing possible solutions with the top plate manufacturer in January. However, shortly after Chinese New Year (that spanned throughout February) the top plate manufacturer let us know they were bailing on the project. Reasons aside, it didn’t only mean we wouldn’t have a solution for the flush fit issue but also didn’t have a manufacturer to make the entire top plate.
Thankfully the top plate manufacturer was very cooperative in transferring the mold and information to a new supplier we had sourced. The new supplier went to work straight away on providing solution. They had a positive result by the end of March. Honestly, I was surprised how fast the process went, but it's not the end of it.
The Engineering Validation Test (EVT)
With the top plate issue seemingly solved, we were able to continue with the Engineering Validation Test (EVT). I also quickly followed up and directed all focus on procuring (purchasing) all the components needed to mass produce Wooting two HE batch 1. More on this later.
--- Context---
We had already gone through the EVT, Design Validation Test (DVT), Production Validation Test (PVT), and Mass Production (MP) with the Wooting two LE. Under normal circumstances, we could just continue with another MP for subsequence productions.
However, since there are a few differences between the LE and HE when it comes to packaging, PCBA, and now also plate, we need to repeat all the steps to ensure we don’t run into any problems during MP or when you receive the keyboard.
Relative to the Wooting two LE, the EVT, DVT, and PVT for the Wooting two HE are more formality than major hurdles. If the EVT checks out, everything else will work out just fine, as it’ll be on equal footing as the LE.
The differences on the Printed Circuit Board Assembly (PCBA) is limited to the total count of components we use. We made a change in our design that removes a few components and lowers down the cost.
Due to the PCBA changes on the Wooting two HE, the EVT keyboards produced slightly different results when going through our quality assurance process for analog input. We had some back and forth communication with the engineers in China running our tests to make sure that it was not the top plate causing the differences.
We’re not able to test this ourselves as fast, since we have a custom-made analog testing machine running on our software at the factory that can check all keys within 10 seconds. When this was resolved, the EVT samples were sent our way for a double-check.
We received the EVT samples last week and are still conducting a few double checks. The whole Wooting Analog Movement app and some logistical preparations had consumed most of the team’s time last week, preventing us to scrutinize the EVT samples. Until so far the top plate and PCBA changes are all within our specifications.
2nd of May update: We confirmed the EVT. DVT will complete mid-May, which will finalize the product approval process. We already passed the pre-EMI test.
But there was one concerning part, the flush fit issue wasn't completely resolved. It's clean around the edges, but now there's a slight raise around the front and back middle section of the keyboard.
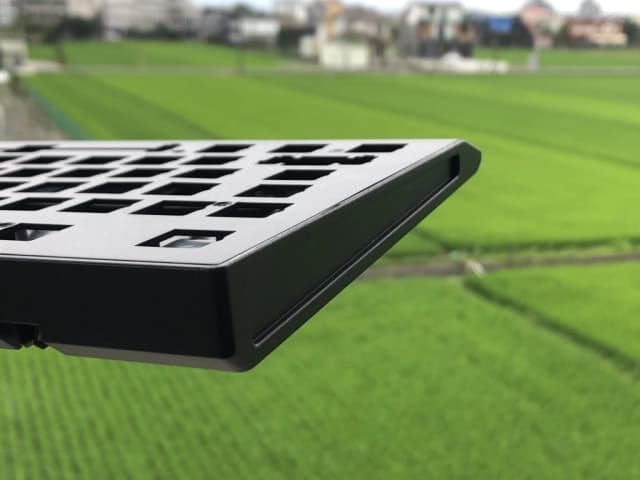
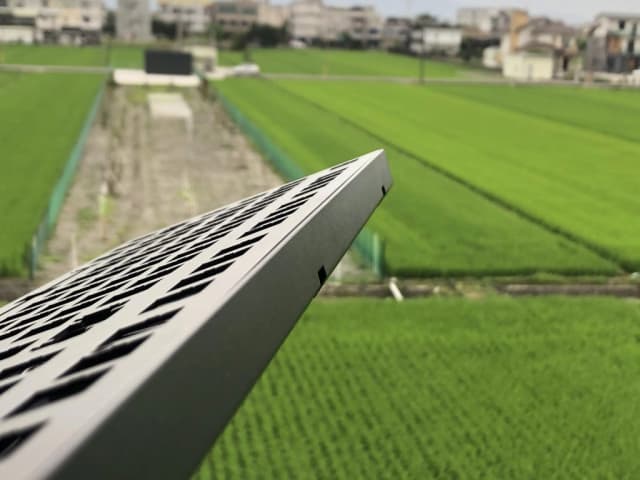
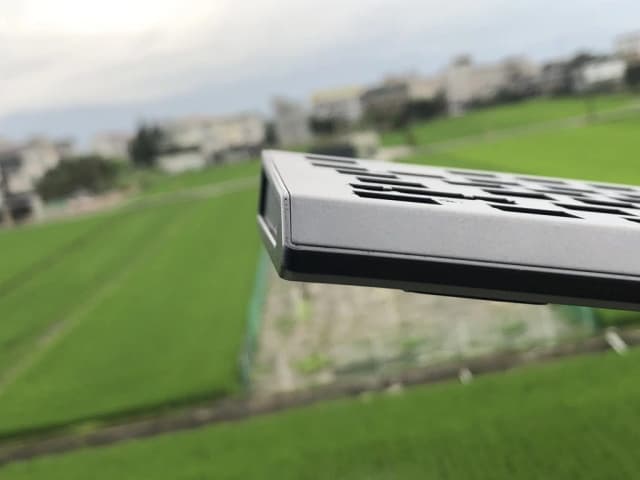
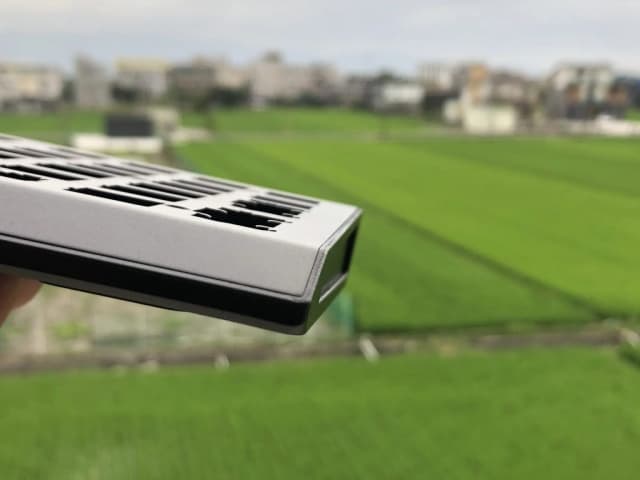
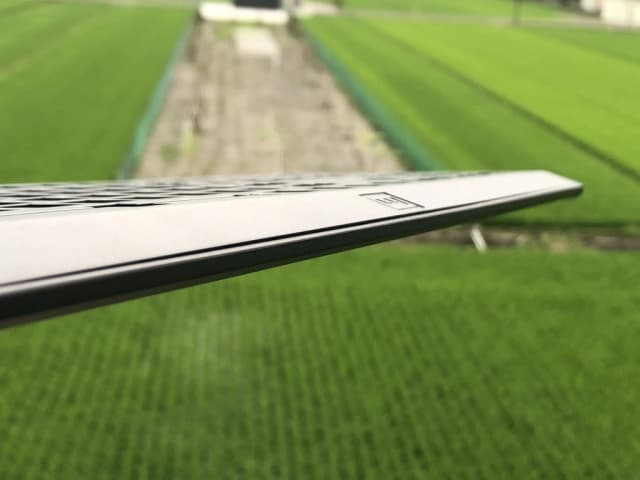
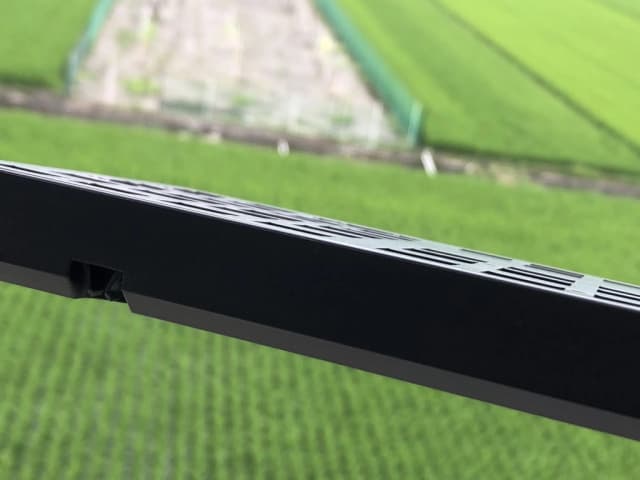
There’s a suggestion from the manufacturer to modify both the top plate mold and bottom case mold to solve it. At the time of writing, I’m still assessing the best move here based on the lead time, cost, and chances of success.
22 Apr. Update: We just got back the quote and lead time. It's only 5 business days, within our budget, and nothing drastic. We're going to get it solved 👍
The procuring IC parts challenge
One of the reasons a lot of electronic products are out of stock is due to the high demand and severe under-supply of Integrated Circuits (IC) parts. The PCBA has a few dozen different IC parts from different suppliers. If only one of those suppliers can’t deliver the IC, no matter how irrelevant, you can’t go into production.
Under normal circumstances, you don’t start purchasing any of the parts until you finished the DVT phase. In this situation, we’re skipping the formality and took the risk of purchasing all the parts in advance.
This is called a “Risky buy” because if it ends up that you can’t use the part, it’s a sunk/non-recuperable cost. We’re not too worried, since we had already gone through MP and 98% of the parts are the same.
To give an example. I had already placed the purchase order for Hall Effect sensors for this Wooting two HE batch 1 production back in September, 2020.
--- Context ---
The Lekker switches are Hall Effect switches also known as Magnet switches. This means that there’s a magnet inside the switch and a sensor on the PCBA that can detect the proximity of the magnet. This sensor is a Hall Effect sensor, the phenomenon is called Hall Effect.
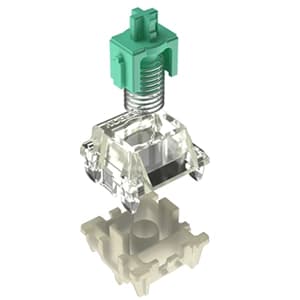
These sensors were delivered last January. Do the math, 4 months lead time. I was informed in December, 2020, that the lead times would increase to 6 months(!). I immediately proceeded to purchase more Hall Effect sensors for the Wooting two HE Batch 2 planned on June, 2021.
It’s already financially difficult for a small company to pre-purchase a large amount of stock to avoid long lead times. Let alone to predict demand that is 8 months in the future (production + ~1.5 months lead time to the warehouse). At this time, I purchase based on non-rosy-colored and reasonable estimates that don’t put us in a financially awkward position.
This is also why I recommend anybody considering the Wooting two HE, to just place the pre-order for the fastest delivery. Not only does it secure you a position, it also immensely helps us predict demand and schedule the next production that’s at least 6 months in the future(!).
Lead time status
Around mid-March, I placed focus on getting procurement going for all the remaining parts and continue with a risky buy. This process involved double-triple-quadruple checking all the IC parts. In the meanwhile, I asked for the approximate lead times on different IC parts. It wasn’t pretty, all components had about 6 to 12 months. Gulp.
I knew about the huge backlog that was building up in the chip industry and had in anticipation already secured the Hall effect sensors and our MCU. But a lot of the common parts are also heavily influenced. It won’t matter if 99/100 components can be delivered by tomorrow, if a single component can’t be delivered for 6 months, it delays everything for 6 months.
Not to fear, these lead times are suggestive. Once the purchase order is placed, you can get realistic lead times. At this time I’m still waiting for a full feedback report on all the lead times. For now, no doom scenario yet, we only hit a problem with 1 component at this time.
A Texas Instrument Multiplexer IC. Comically the exact type of component you’d expect issues with since the industry IC backlog was worsened by the severe weather conditions in Texas, where a lot of IC manufacturers have a location. The expected delivery time? November 2021. Great…
Thankfully, the multiplexer component is replaceable, it’s a common type of part. We need to find an available, alternative brand part and test it on the current PCBA for verification before we move on to the DVT phase.
22 Apr. Update: We're able to find parts on-stock and doing procurement with 3rd parties. This means we circumvent the regular route and purchase at higher cost from external vendors. Work in progress, but it's looking good.
2nd of May, update: We procured on-stock items for essential parts and are in the process of transferring it to the factory.
This is all fresh information. It’s also the reason why it’s taken so long for me to publish a followup update. The situation keeps fluctuating and future dates keep getting pushed by new situation that present themselves in the present. If I update based on every moment I have new information, trust me, you're going to suffer some serious emotional swings :)
Batch 1 or 2 - what can I expect?
If you placed an order before the 18th of March, then you’re in Batch 1. If you placed an order after the 18th of March, you’re most likely in Batch 2. If an order gets canceled in Batch 1, we move the earliest Batch 2 order in its place.
At this moment, we are not able to preview live on a per order basis of what batch you’re in. This makes it difficult for us to give a quick answer on which batch you are in. We’re still working on a better system, but honestly, I don’t think we have the spare resources (time to work on it) for the next 2 months. I will do a manual check in the course of next month (May) and send out an update email to everybody with their batch number as of date.
In all cases, to repeat what I mentioned earlier in this update; if you pre-ordered the Wooting two HE, you’ve secured a keyboard and will have the earliest possible delivery date. If you wait it out, you’re likely going to be out of luck. Batch 2 is likely to sell out before we can make the delivery and we have at this time not planned Batch 3 yet looks at lead times.
Delivery date - Batch 1
If you read the rest of the update, then you’ll know that I can’t estimate the new manufacturing date. The reality is that the MP date is not set in stone yet, due to the procurement and verification steps. There are suddenly a few new challenges to be solved and decisions to be made. What I can tell now is that May is not going to work out.
If I want to be on the safe side, I should just delay the shipment estimation to July 2021. That’s a June production. That would set better expectations and if we have favorable winds, then I can share good news for a change.
Delivery date - Batch 2
This batch entirely depends on the hall effect sensor delivery of the Hall effect sensors. I had already given the green light for the procurement of all the IC parts (including that Texas Instrument part that will change) and am waiting for the EVT confirmation to also procure the smaller electronic parts (like capacitors). So as we solve Batch 1 challenges, it’ll also solve it for Batch 2.
At this time we expect the Hall Effect sensors to deliver by mid-May. Depending on how things turn out, we might produce it at the same time as batch 1. The shipment estimation is July 2021.
Faster delivery options
Current world circumstances have made logistics a little more challenging. Lately, I calculate all our costs and budgets based on using sea freight to our warehouses. I often use faster transport methods when we need to supplement a small amount of stock. When it comes to the pre-orders it’s a bit tricky. I’m not able to split the pre-orders into different shipment methods and deliver them at random to different people. It’s either all this way or all the other way.
When the pre-order reach a certain larger amount, I automatically opt to ship everything by sea freight to our warehouses. This is the slowest but most affordable transport method for larger loads. It takes about 35 to 40 days in transit, excluding the additional communication that goes beforehand. But this option has become less and less desirable due to the peak traffic, congestion, and overworked ports. Let alone, when a Suez canal situation comes on top of it. That added a month delay to all the EU Wooting two LE backers 👀.
The alternative transport method is air freight. This is similar to express couriers (UPS, FedEx, DHL, etc), but then for large freight. It’s still 4-8 times more expensive than sea freight. At this time, it’s peaking due to high demand and low supply of commercial flights (which often also carries freight cargo). This takes about 10-15 days, excluding communications.
Only for the EU store, we have an alternative that sits in between these two options, rail freight. It’s slightly more expensive than sea freight (1.5-2x) and takes about 20 to 30 days, excluding communications. I’m still slapping myself for having forgotten this option for EU Wooting two LE orders in the midst pressure of getting everything arranged.
I have learned from previous shipments, that some of you are willing to pay an additional amount for faster delivery. And we can save a lot of time by opting for air freight instead of sea freight (cuts 70% / ~25 days). That’s why I’m planning to reserve a limited quantity to ship by air freight that people can opt to buy into. I expect the cost to be an additional 10 USD/EUR per keyboard. This is a lot more efficient than paying for faster (expedited) last-mile delivery (saves 5 days with +20 USD).
At this time, there’s no action you can take and it’s not available yet. When I’ve settled on the production date, I’ll start to arrange all the details and follow up on this.
Zen mode
Making our products from scratch exposes us to a lot more of the manufacturing process elements. Including the suppliers, stock, and quality assurance. It’s complicated, requires a lot of communication, and problem-solving.
This is especially the case when developing a new model — the Wooting two LE was one of our most challenging projects. When it was successfully mass-produced, it was a huge sigh of relief and I thought we could start running a few smooth productions for the Wooting two HE. But I was to be proven wrong — again.
Nature of the business 🤷♂️. Thankfully we’re always up to the challenge, as long as you retain faith in our work.
Much <3,
Calder
Co-founder & CEO
© 2025 Wooting technologies版权所有。